RC modely
CNC fréza G2
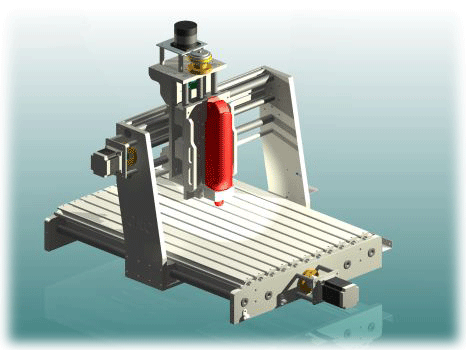
Základní technické údaje
|
Proč CNC fréza
Modelář stále potřebuje pro svou potřebu nějaké kulaté a hranaté díly. Ne vždy se dají koupit a pokud už ano, cena je díky malému Českému trhu neúměrně vysoká. Při návrhu a výrobě našeho HeliXu jsme některé díly navrhovali s tím, že se budou vyrábět na CNC stroji. Mít ale CNC vlastní byla výzva. Nejdříve jsem hledal na WEBu. Cena, za kterou se výrobky nabízejí mi připadala nedostupná. Po analýze konstrukčních prvků mi některé i profesionální výrobky přisly mechanicky nedostetečně tuhé. S několika jsem si i setkal a předtucha byla bohužel skutečností. Další možností je sehnat plán a podle něj stroj postavit. Problém to však nevyřešilo. Výroba mnohdy vyžadovala speciální přípravky nebo materiál.Proto mi jako jediný vhodný způsob přišlo si narhnout frézu sám. Samozřejmě s využitím nějakého 3D CAD systému. Naštěstí mám možnost pracovat, byť ne profesionálně, s produktem Autodesk Inventor.
Návrh první verze
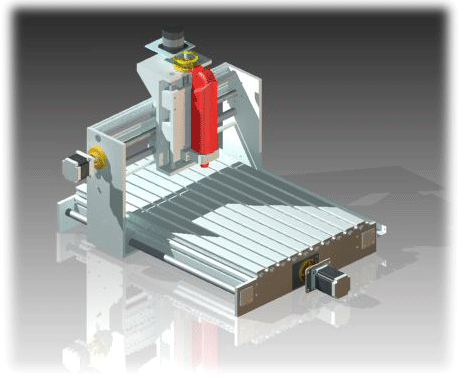
Poté jsem po večerech zasedl k notebooku a modeloval a modeloval. Za několik týdnů jsem měl připravené výkresy a mohl přistoupit k výrobě.
Výroba
Duralové díly jsem navrtal na fréze s číslicovým odečítáním polohy. Pouze otvory pro vodící tyče jsem nenavrtával. Přední a zadní čelo osy X a levá a pravá bočnice osy Y jsou zrcadlově stejné. Tyto díly jsem svrtal dohromady a pevně sešrouboval. Ostatní otvory jsem vrtal až v tomto stavu. Dobře nabroušený vrták neměl kam uhnout a tím jsem ušetřil spoustu času na velké souřadnicové fréze. Tu jsem použil znovu až k odvrtání otvorů vodících tyčí. Výsledný přesný otvor vznikl výstružníkem.Z Inventoru jsem měl seznam spojovacího materiálu a vyrazil jsem nakoupit potřebné šrouby. Ne vždy bylo jednoduché je sehnat. To bylo naštestí pár šroubů se speciální nízkou imbusovou hlavou. Nejhorší prací bylo vytočení mnoha závitů. Připadal jsem si jako Ch.Chaplin ve známém filmu.
Nejprve jsem celou frezu lehce složil abych měl jistot, že jsem někde neudělal chybu. Pak ji znovu rozebral a namontoval koncové mikrospínače. Natahal jsem přívodní dráty s dostatečnou rezervou v délce a celou frézu složil dohromady. Doplnil ji uchycením energetických řetězů a několika týdnech bylo vše hotovo. Chyběla ještě výkonová elektronika.
Aby se dostal signál z počítače až do krokového motoru, musí projít docela složitou cestu. Krokové motory mají většinou 8 vinutí. Ty se pak spojují buď sériově nebo, pro větší výkon, paralelně. Každé vinutí bývá značeno barevně a k motoru je vždy schéma zapojení. Pokud není, pak nastává poměrně netriviální na které vinutí ten který drát vede. Výkonová elektronika posílá postupně proud do jednotlivých vinutí. Máme-li čtyři vinutí, které sepneme postupně, motor udělá tzv. jeden celokrok. To je 1.8 stupně. Tedy na jednu otáčku je to 360 / 1.8 = 200 pulzů. Takhle bychom ale s pohonem spokojeni nebyli. Je moc hrubý. Proto se používá tzv. mikrokrokování. Tady záleží na elektronice jak jemné mikrokrokování je schopna udělat. V principu jde o to, že místo abychom jedno vinutí odepli a další připnuli, rozsekáme každý pulz na řadu menších a na dvou sousedních vinutím postupně proti sobě měníme střídu. Tím se rotor plynule otáčí. Toto zapojení se ještě kombinuje s tzv.choprováním, kdy se snímá proud v jednotlivých vinutích a přepouští se s pomocí rychlých diod. Toto řešení dramaticky snižuje protékající proud při zachování točivého momentu.
Do motoru pouštíme tedy dost velké napětí (typicky 24-47V) a docela slušný proud (rozhodně ale ne takový jako do pouštím do regulátoru Trex500). V počítaci máme k dispozici TTL logiku s rozsahem 0-5V a proud několik mA. To nám dává paralelní port. Ten má tu výhodu, že kromě výstupních pinů má i vstupní, které se používaji na koncové spínače a čidla. Aby byl počítač chráněn od možného poškození ze strany řídící elektroniky, bývá (a měl by být) opticky oddělen. To znamená, že ani zemní vodiče frézy a počítače nejsou spojeny. Optické oddělelní zajistí prvek - optočlen. Takové desky se dají koupit, ale nenašel jsem rozumnou, která by oddělovala všechno. Jak výstup, tak vstup. Nastoupil Google a hledal nějaké zapojení. Výsledek - nejlépe je navrhnout si desku sám. Je opravdu zajímavé s jakými názory se člověk v různých fórech setká. Co všechno musí být stíněno a proč, proudové smyčky málokomu něco říkají. Neviním je z neznalosti ale z toho jak mnohdy trvdě trvají na svých pravdách. Pro neznalého je problém najít zrníčko pravdy.
Pro umístění elektroniky jsem použil starou serverovou škatuli. Ta měla totiž na vstupu větráčky doplněné i mikrofiltry a ty vytváří uvnitř přetlak. Každý víte, jak vypadá domácí počítač uvnitř po roce používání, natož v prachu dílny. Stejný case jsem zvolil pro řídící počítač.
Z jiného počítače, stařičkého sálového počítače, byl ve sklepě nepoužívaný stojan, který jsem předělal na stojan pod frézu. Po téměř více jak půl roce práce nám stojí vedle soustruhu i malá CNC fréza a já se začínám učit G-kód (příkazy pro ovládání frézy). Nejhorší etapou jistě bude sehnat vhodné programové vybavení. Naštěstí ten hlavní řídící je pod Linuxem. Kdybych měl větší prasátko, tak bych ale sáhl pro Mach3.
![]() |
![]() |
celkový pohled | vřeteno Kress |
![]() |
![]() |
spojení X motoru | energetický řetěz |
![]() |
![]() |
výroba desky HeliIX | výroba desky HeliIX |
![]() |
![]() |
výroba desky HeliIX | hotové díly HeliIX |
Verze G2
Na první verzi jsem si vyskoušel, že stroj pracuje jak má a že má smysl do něho ještě něco investovat. Navíc pro její výrobu se dá s úspěchem použít stávající stroj. Tím pádem jsem nebyl omezen jen na vrtačku a frezu s číslicovým odečtem, ale mohl jsem všechny díly vyrobit na CNC fréze. To mi umožnilo navrhnout zapuštěné otvory a tím některé ložiskové jednotky více schovat, čímž jsem zmenšil přečnívající díly.S výhodou jsem využil vlastnosti se kterou jsem původní frézu navrhoval, tedy aby všechny díly ze kterých je fréza vyrobena šly na této fréze vyrobit.
Také jsem změnil propojení koncových dorazů a všech vstupů a výstupů do jednotných konektorů CANON. Změnu doznaly i konektory připojující vlastní motory. Šroubovací, které jsem použil dříve nebyly nejvýhodnější. Současnou verzi jsem osadil 4pinovými konektory se západkou a pojistkou. Na oddělovací desce jsem vyměnil optočleny za výrazně rychlejší, tedy i dražší, a dosáhl tím bezpečné zrychlení motorů.
Stroje vyrábějí stroje
![]() |
![]() |
Frézování zaoblení | Čelní deska |
![]() |
![]() |
Bočnice | Nová deska vřetene |
Co fréza dokáže
![]() |
![]() |
Plošný spoj "Battery meter | JETIbox mini držáček na anténu |
![]() |
![]() |
astronomická montáž HS-1 | Aztécký kalendář (mosaz průměr 65mm) |
2.VI.2012 |